While playing golf, have you ever wondered how a golf ball is made? For most of us, we tend to focus particularly on choosing our clubs, but what about its pair?
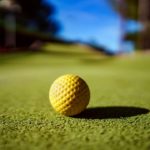
Below, we will discuss the step-by-step process of how a golf ball is made and its construction.
How a Golf Ball is Made | Step-by-Step Process
Like with most golf ball equipment, how are golf balls made is also a tedious process.
Throughout history, the procedure of how golf ball is made has been continuously altered and modified to what it is today.
From using beech wood to chicken or goose feathers, the material used for producing golf balls has come a long way.
Today, how golf balls are made often involves the use of rubber and plastic materials. It also has a unique design that supports its aerodynamics and trajectory.
That said, here are the details on how are golf balls made that you will find helpful:
Golf Ball Raw Materials
As mentioned, modern golf balls now consist mostly of rubber and plastic materials.
During the ’70s, using a petroleum-based polymer called polybutadiene became the trend, improving the golf ball’s interior.
But because it was excessively soft, researchers tried to find a way to strengthen the material. What Spalding has found was that using zinc addresses this issue.
After its incorporation with polybutadiene, it has become the standard material for golf balls.
The materials used for the standard golf balls vary a little bit depending on their type. But the commonly used golf ball types are two-piece and three-piece golf balls.
Here are the common materials used for a two-piece and three-piece ball:
- Two-piece: Durable ionomer resin cover and solid rubber core formed into a sphere
- Three-piece: Balata or ionomer rubber cover and liquid-filled with thread wound or solid rubber core
Golf Ball Manufacturing Process
Now that you know the common materials used in how golf balls are made, let’s proceed to the manufacturing process.
Note that this is the standard process for all types of golf balls and not a single type.
Multi-layered golf balls can take up to 30 days to finish, while those with one to two layers require fewer hours.
With that, here is the step-by-step manufacturing process of how are golf balls made.
Core Molding and Formation
The molded core of the golf ball combines different materials that give a chemical reaction to rubber compounds.
Upon applying heat and pressure to the materials, it will start forming the center of the ball around 15 inches.
Cover and Dimples Formation
To form the cover and dimples of a golf ball, you need to use either compression molding or injection molding.
Here are the processes of how golf ball is made depending on the molding type used:
Compression Molding
- The cover will undergo injection molding into hollow hemispheres through the core.
- It then undergoes heating and pressing using a compression mold. This process will fuse the molded cover over the core while forming the dimples.
Injection Molding
- Using pins, the core is positioned within a mold cavity.
- Then, you inject molten ionomer resin into the core’s dimpled cavity.
- The pressure and heat from this procedure result in cover and core fusion, with the center forming the dimples.
- Upon cooling and hardening of the resin, you retract the pins and remove the balls.
Polishing, Painting, and Coating
In this procedure, the rough spots on the cover are polished. The machine will then apply paint coating to the ball by placing it on a spinning post for even painting.
The device used for applying the paint is automatic spray guns. Then, the machine will stamp the surface of the ball with the brand’s logo.
To ensure scuff resistance and great sheen on how a golf ball is made, the final step is applying a clear coating.
Drying
After applying the paint, the machine will load the balls into different containers and place them in large dryers to dry.
Packaging
Once the golf balls are completely dry, the machine will now package them in boxes and plastics. The packaging varies depending on the brand.
Golf Ball Quality Control
The manufacturing process of how a golf ball is made doesn’t end there. Besides this tedious procedure, golf ball manufacturers employ the use of computers and X-Ray machines to ensure a perfectly round ball.
The quality control framework is a crucial part of any golf ball manufacturing procedure.
With that, here are the standard quality control methods on how a golf ball is made:
Compression Ratings
Manufacturers use compression rating to measure golf balls that underwent compression molding.
It calculates the restitution coefficient or the golf ball’s relative velocity bounce to that of the preceding bounce. Note that this method doesn’t apply to two-piece balls, which uses a co-efficiency rating.
This measurement is the ball’s initial speed ratio against the return speed after striking a metal plate.
Mechanical Testing
On the other hand, manufacturers use mechanical testing for verification that the performance of the ball complies with the USGA’s standards.
They use different testing equipment to measure the ball’s performance from various angles.
Iron Byron
The Iron Byron or True Temper Mechanical Golfer takes inspiration from Byron Nelson’s swing.
The machine can fit any club, and you can also set the settings for different swing speeds. It has a configuration catered to a driver and 5- and 9- irons for standard testing.
Ball Launcher
Meanwhile, the Ball Launcher is able to launch golf balls at different launch angles, spin rates, and velocity.
Testing different launch conditions allow manufacturers to determine the best skill the golf ball caters to.
Wind Tunnel
Some golf ball manufacturers use wind tunnels for identifying lift action and wind resistance of the golf balls.
Golf Ball Measurement and Analysis
The quality control team will then measure and analyze the data gathered (associated with ball flight) from using this equipment.
It looks into the carry distance, rolls distance, total distance, apogee angle, and the statistical accuracy area (SAA).
Here are how manufacturers measure these:
- Carry distance: This is the distance of the golf ball on the flight. They measure this through a marked grid system in the landing area.
- Roll distance: You calculate this by subtracting the carry distance from the total distance.
- Total distance: This is the distance of the golf ball on the flight with the addition of the roll distance.
- Apogee angle: This is the trajectory height that the golf ball reaches on a flight. They measure this through a high-technology camera with a telescopic lens.
Using its gridded monitor, it points down the conjunction range.
- Statistical accuracy area (SAA): The SAA is also called the dispersion area used to measure a golf ball’s accuracy. The value of the SAA bases on the ball performance’s deviations in the carry direction.
They will then calculate this to come up with an elliptical landing area.
More About Golf Balls
Now that you know how a golf ball is made, let’s delve deeper into the details of the golf ball. Beneath the cover, a golf ball has a lot of engineered structures that help boost your game.
With that, we will talk about the components of the golf ball in this section. You will also discover the jaw-dropping number of how many golf balls are made each year.
Core
The core of the golf ball is generally made of rubber or liquid center.
This material may combine metals like titanium or tungsten, or acrylate, which is a plastic-like material. All golf balls have different core compression, ranging from 80 to 100.
Here are the three different core compressions.
- 80 compression: Best for women and seniors
- 90 compression: Best for the average golfers
- 100 compression: Best for professionals and advanced golfers
Cover
It is the outer layer of the golf ball that is covered by dimples. Here are the different materials commonly used for golf ball covers:
- Balata
- Surlyn
- Urethane
Dimples
The reason for the indentation of dimples on the surface of a golf ball is primarily for a good flight.
Unlike when you use a smooth ball, the dimples cut down the drag when the ball is in the air. The dimple numbers, size, and pattern vary from different models and different brands.
Weight and Size
The USGA regulation states that a golf ball must weigh at least 45 grams or less while the diameter should at least be 1.68 inches.
There is no set minimum weight and no set maximum size for golf balls. But with scientific backing and testing, manufacturers would produce golf balls within the standard size.
How Many Golf Balls are Made Each Year
In recent years, there has been no decrease in the number of people playing golf. How many golf balls are made each year is thanks to this.
That is why manufacturers continually develop innovations to meet new and experienced golfers.
From the distance, control, feel—there is a myriad of aspects technology can improve. As of writing, there are more than 80 different golf ball models with varying designs and construction.
With that, the total number of how many golf balls are made each year is a whopping 1.2 billion.
On the other hand, how many golf balls are made each year in the U.S. is 850 million. The sales of golf balls alone make up $450 million annually across the United States.
More shockingly, the entire golf industry reaps a total of $25 billion each year in America.
Thus, despite all the changes in golf ball construction and technology, there remains an upswing in the golf ball market.
From the Core to the Case
Each process of the golf ball construction can dictate how it will perform in the course.
From the materials used to the manufacturing process, it will all matter once you hit your shot.
Thus, it is vital for all golfers to know how a golf ball is made.
This knowledge will help you make better choices on what golf ball to purchase.
It will help you look for golf balls with features that meet your needs, strengths, and weaknesses.
We hope this article helped and remember to examine your golf ball—from the core to the case.
More Information
Last Updated on December 4, 2023 by Paul Roger Steinberg